We help the world since 2012
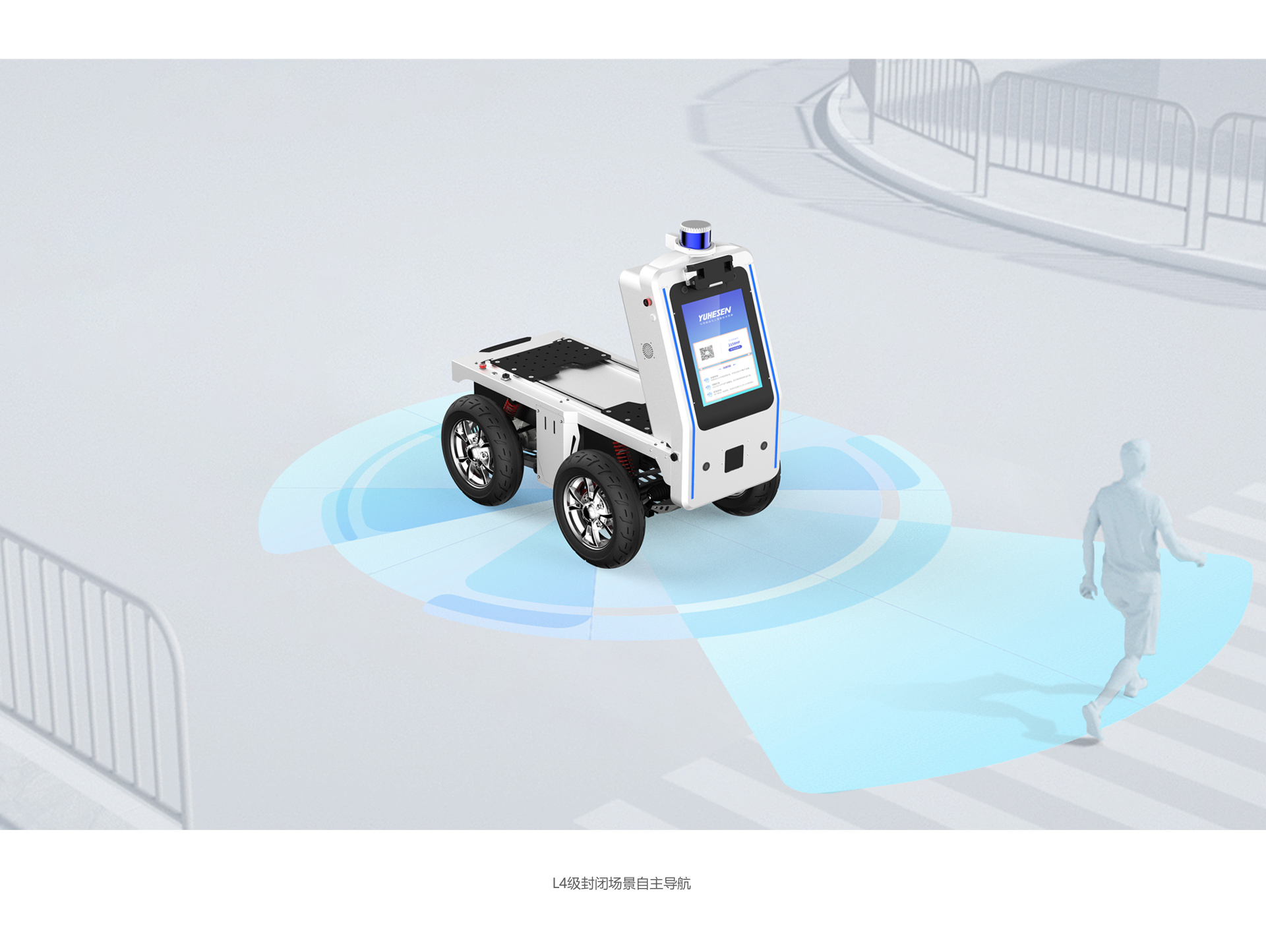
AGV vs AMR: What’s the Difference?
Our team is doing research on power module for further applucation and find that there are some people don’t understand AGV and AMR.
As automation continues to shape the future of industries such as logistics, manufacturing, and warehousing, the use of robotics has become essential to improving efficiency. Two types of robots stand out in this realm: Automated Guided Vehicles (AGVs) and Autonomous Mobile Robots (AMRs).
What’s AGVs ?
An automated guided vehicle (AGV), different from an autonomous mobile robot (AMR), is a portable robot that follows along marked long lines or wires on the floor, or uses radio waves, vision cameras, magnets, or lasers for navigation. They are most often used in industrial applications to transport heavy materials around a large industrial building, such as a factory or warehouse.
What’s AMR ?
Autonomous Mobile Robots (AMRs) are advanced robotic systems designed to navigate and operate in dynamic environments without human intervention. Unlike Automated Guided Vehicles (AGVs), which rely on fixed paths for navigation, AMRs use various technologies such as sensors, cameras, and artificial intelligence to understand and interact with their surroundings.
Differences between AGV & AMR
From the definition, you will find that they both share a common goal of optimizing workflows, however, their methods of operation, navigation, and power requirements differ significantly.
1. Navigation Technology
One of the most fundamental differences between AGVs and AMRs is their approach to navigation.
- AGVs rely on external guidance systems to follow pre-determined paths, which could involve magnetic strips, wires, or laser systems. They are highly dependent on infrastructure, making them effective in structured environments where movement is predictable and repetitive. However, this also means they are less flexible when changes or obstacles arise.
- AMRs, by contrast, use advanced technologies such as sensors, cameras, and real-time mapping algorithms to navigate autonomously. These robots don’t need fixed paths, allowing them to operate in dynamic environments where layouts frequently change. AMRs can adjust their routes based on obstacles or optimize their paths for efficiency, giving them greater flexibility than AGVs.
2. Flexibility and Adaptability
AGVs are well-suited for environments where the workflow remains constant. Their reliance on fixed paths makes them ideal for tasks like transporting materials in factories, but it also means they require significant infrastructure investments and are less capable of adapting to changes.
AMRs, on the other hand, are built for adaptability. Whether it’s avoiding a sudden obstacle or adjusting to a new warehouse layout, AMRs can seamlessly adapt to their environment. This makes them a perfect fit for industries like e-commerce or service sectors, where agility and responsiveness are critical to success.
3. Cost of Deployment
Because AGVs require physical infrastructure such as tracks or guiding systems, the initial setup costs can be high. Maintaining and updating these systems adds to the cost over time, making AGVs less scalable for businesses with evolving needs.
In contrast, AMRs do not rely on external infrastructure. Their ability to map and understand their environment autonomously reduces deployment costs and offers scalability for businesses planning to grow or change their operational layouts. This ease of deployment makes AMRs an attractive choice for industries that need to adjust workflows regularly.
4. Power and Energy Efficiency
Both AGVs and AMRs have specific power requirements, but the efficiency of these systems can vary significantly.
- AGVs tend to consume more power because they are constantly in motion following set paths. They require robust energy systems to maintain their repetitive operations, which can lead to higher energy consumption over time.
- AMRs are generally more energy-efficient due to their ability to optimize routes and navigate intelligently. Their advanced systems allow them to conserve energy by taking the most efficient paths, which reduces the demand for frequent charging and lowers overall energy costs.
5. Energy Density, Voltage, and Current Requirements in AMRs
When it comes to powering AMRs, the key requirements include:
- Energy Density: AMRs need power modules with high energy density to ensure longer operation times between charges. Given the dynamic nature of their tasks, energy efficiency is crucial to prevent frequent downtime.
- Voltage and Current: The electrical systems in AMRs must support stable voltage and current to ensure smooth operations. The voltage and current requirements vary depending on the size and complexity of the robot, with more advanced AMRs requiring robust power supplies to support their sensors, motors, and navigation systems.
- Efficiency: AMRs are designed to maximize efficiency. DC-DC converters with high efficiency (90% or above) are essential for minimizing energy loss and reducing heat generation. Efficient power systems allow AMRs to operate for extended periods while maintaining peak performance.
- Size Constraints: AMRs, especially in compact or mobile designs, require small-sized power modules that pack significant power output into a confined space. This compact design is critical for ensuring the robot’s agility while maintaining stability and balance during movement.
6. Applications in Logistics and Services
In terms of applications, AGVs and AMRs have found their respective roles in automation.
- AGVs are commonly deployed in large manufacturing plants or warehouses where the workflow remains consistent. Their ability to follow fixed paths makes them ideal for moving large volumes of goods in predictable environments.
- AMRs, on the other hand, excel in more dynamic settings like logistics centers, e-commerce fulfillment, and service industries such as healthcare. Their ability to navigate complex and changing environments means they can carry out tasks like order picking, goods transportation, and even customer or patient deliveries.
Which Is Right for Your Business?
When comparing AGVs and AMRs, the choice depends largely on the nature of your operation. AGVs are best suited for controlled environments with repetitive tasks, where a well-established infrastructure can be used. Meanwhile, AMRs offer greater flexibility, adaptability, and scalability, making them ideal for industries with dynamic workflows and changing environments.
As companies continue to evolve, the adaptability of AMRs presents a strong case for businesses looking to future-proof their operations. Additionally, selecting the right power solution—with the right energy density, voltage, and efficiency—is critical for ensuring that AMRs deliver consistent, high-performance results.
At CHONDA TECHNOLOGY, we specialize in manufacturing modular power supplies. Whether you are utilizing AMRs or AGVs, our power modules can enhance your operations. Feel free to reach out to us for more information!