We help the world since 2012
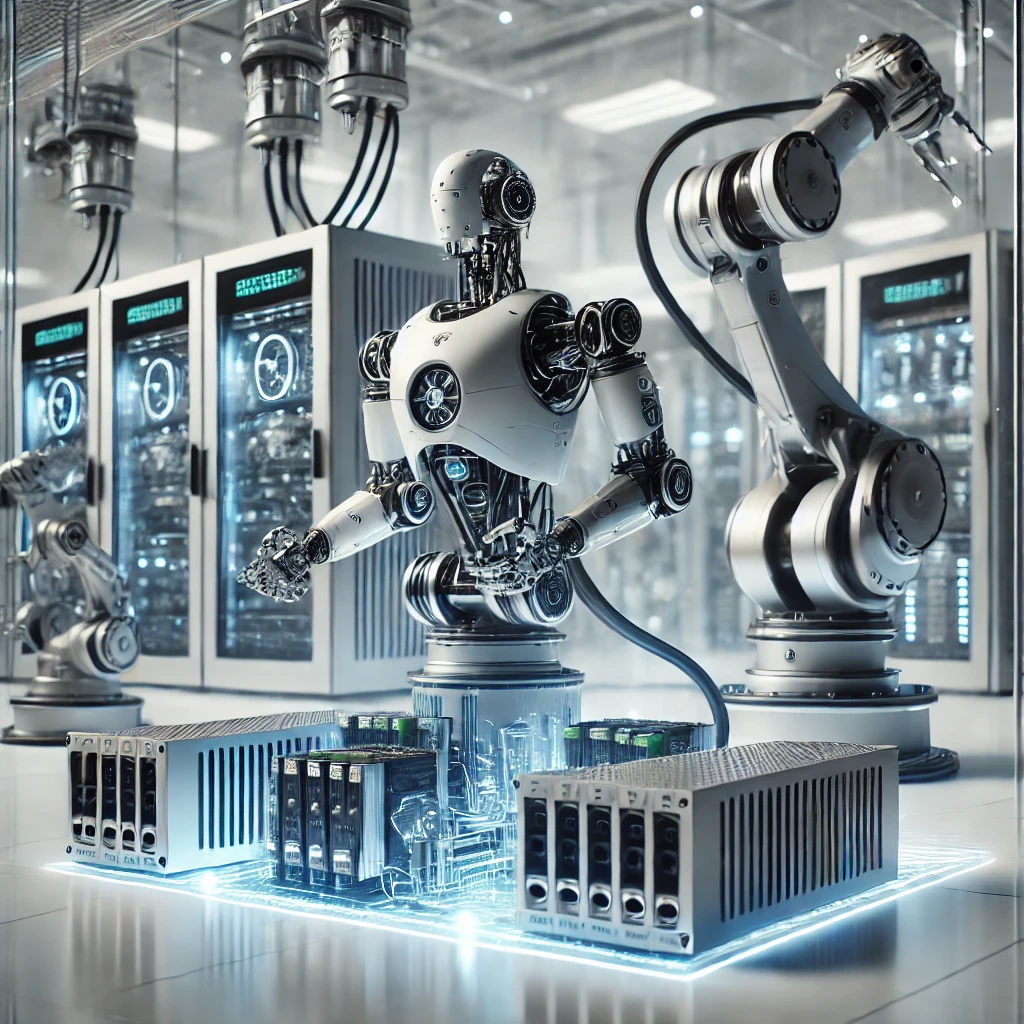
Robot power systems: how to choose the right DC-DC converter
In modern robotics, power management is one of the key factors to ensure the performance of robots. robotics DC-DC converter, as an important part of the power system, can efficiently regulate the voltage to provide robots with the power they need.
CHONDA TECHNOLOGY will discuss the role of robotics DC-DC converters in robot power systems, especially in applications such as industrial robots and medical robots, and provide guidance on selecting the right DC-DC converter.
The Role of robotics DC-DC Converters in Robotic Power Systems
A DC-DC power module is a power management device that converts an input voltage to a desired output voltage. Power converters enable innovation in robotic applications. Its main role in a robot power system is to provide a stable power supply to various components.
For example, in industrial robots, DC-DC converters provide a stable voltage to motors, sensors, and control systems to ensure efficient robot operation. In medical robots, the stability and efficiency of DC-DC power supply are particularly important, as they must operate under precise and reliable conditions to ensure patient safety.
The Importance of Choosing High-Efficiency DC-DC Converters
Most semiconductor components can only operate at DC. Therefore, electrical products that operate in sockets require an “AC/DC converter” that converts AC (alternating current) 100V to DC (direct current).
The ICs on the circuit boards of the entire machine have their own inherent operating voltage ranges and require different voltage accuracy. If power is supplied from a power source with unstable voltage, it may cause malfunctions, degradation of characteristics, or other abnormalities.
Therefore, it is necessary to use a “DC/DC converter” to convert and stabilize the required voltage. The following are some of the key factors:
Input Voltage: Ensure that the DC-DC converter you select is capable of accepting the robot’s power supply input voltage range. Different robot applications may use different voltage sources, and choosing the right input voltage will prevent system overload or instability.
Output Voltage: The output voltage must match the voltage requirements of each component of the robot. For example, sensors may require a 5V supply, while motors may require a 12V or 24V supply. Therefore, when selecting a robotics DC-DC converter, make sure its output voltage range meets the needs of all components.
Conversion Efficiency: A high-efficiency DC-DC converter minimizes energy loss and improves the overall efficiency of the robot. Choosing a high-efficiency power module not only extends the robot’s runtime, but also reduces heat generation and energy waste.
Power requirements for common robots
The power requirements for specific types of robots are determined by the application:
Agricultural Harvesting Robots: Planting, tending, and harvesting crops (fruits, vegetables, grains) can be accomplished through automated vehicle guidance technology coupled with vision recognition and a variety of environmental and soil analysis sensors. These large robotic vehicles are typically powered by high voltage DC power supplies of 400 V or more.
Delivery robots: Deliver a variety of different products to consumers or parks in the last mile. Although the size and weight of the load varies, these robots are typically powered by 48 V to 100 V batteries and have higher runtime requirements than warehouse and stockpile moving robots.
Warehouse Inventory Moving Robots: Perform inventory management and order fulfillment tasks in large warehouse environments. These robots are typically powered by 24 V to 72 V battery power and are randomly recharged as needed.
Our DC-DC power modules: optimizing power management
To meet the need for robotic power management, our company offers a range of highly efficient DC-DC power modules specifically designed for robotic applications. These modules have the following features:
1. Isolation
1, noise isolation: (analog and digital circuit isolation, strong and weak signal isolation)
2, safety isolation: strong and weak power isolation \ IGBT isolation drive \ surge isolation protection \ lightning isolation protection (such as human contact with the isolation of medical electronic equipment)
3, ground loop elimination: remote signal transmission \ distributed power supply system
2. The voltage conversion
Boost conversion\Buck conversion\AC/DC conversion (AC/DC, DC/AC) \Polarity conversion (positive and negative polarity conversion, single power supply and positive and negative power supply conversion, single power supply and multiple power supply conversion)
3. Protection
Short circuit protection, over-voltage protection, under-voltage protection, over-current protection, other protection
4. Noise reduction
Adopt active filtering
5. Voltage stabilization
AC mains power supply\remote DC power supply\distributed power supply system\battery power supply
6. Wide Input Voltage Range
Our DC/DC power modules can accept a wide range of input voltages for different types of robots.
7. Adjustable Output Voltage
We provide flexible output voltage options to meet the needs of various machine components.
8. High conversion efficiency
Through optimized design, our modules have high conversion efficiency, which can effectively improve the efficiency and stability of the robot.
By choosing the right DC-DC power module for robotics, you can significantly improve the performance and reliability of your robot. We are committed to providing our customers with the highest quality power solutions to help you achieve success in robotics applications.